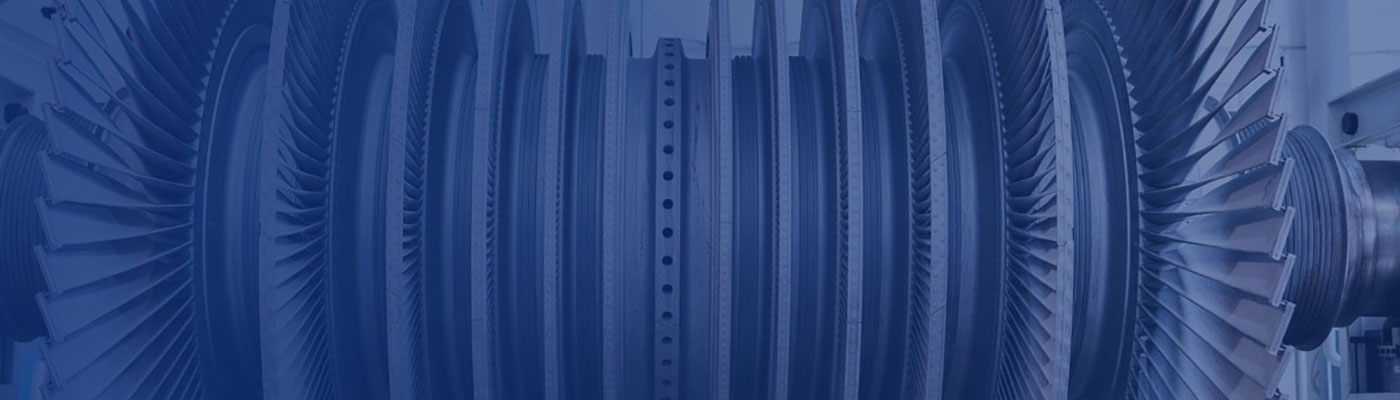
VARTECH™ ISCCLEAN WITHOUT COMPROMISE
Learn how VARTECH™ Industrial System Cleaner (ISC) utilizes proprietary technology to do the most thorough and efficient cleaning job without creating operational constraints.
The Solution: A System component and lubricant-compatible cleaner
The experts at Caltex Lubricants have developed a new cleaning solution to help you protect equipment from varnish and ensure peak productivity in your operation - The VARTECH™ Industrial System Cleaner (ISC).
DEFEAT DESTRUCTIVE VARNISH TO OPTIMISE TURBINE PERFORMANCE. INTERESTED IN VARTECH™ ISC?
Frequently Asked Questions
No. Caltex lubricants with VARTECH™ Technology are specially formulated to incorporate varnish controlling properties into the lubricant. VARTECH™ Industrial System Cleaner is designed to clean systems and uses different formulations.
We does not recommend this approach as:
- Modern lubricants are high performing advanced technology formulations and the chemicals in the cleaner can adversely alter the balance of the formulation which may in turn cause unexpected lubricant upset over time,
- Varnish and other contaminant particles remain in the system until removed with the oil.
VARTECH ISC is designed as an end-of-oil-life cleaner precisely to avoid these issues. Its components are not tailored for long periods of operation such as the multiple years turbine oil is often in service.
VARTECH ISC is available through our network of lubricant distributors. Please contact us .
Many operators choose to use a chemical cleaner as part of every oil change process. Others choose to clean only when operational evidence of varnish deposits are present. Deliberate consideration of whether to clean or not should form part of the planning for every oil change.
Old, degraded oil mixed into the refill oil will diminish the performance of the fresh oil. Residual cleaner will affect both the performance and life of the fresh oil. Some cleaners are so incompatible with fresh oil that they can reduce by ⅔ the expected life of the oil based on Rotating Pressure Vessel Oxidation Test (RPVOT) tests.VARTECH ISC is specifically formulated to be compatible with turbine oils and so minimize the impact of residual cleaner on the fresh oil.
Rinse flushing is a best practice for any oil change to completely remove old, degraded oil from all parts of the system, particularly when any of the following conditions exist:
- Prior to cleaning, the in-service oil was experiencing rapid oil degradation or was extremely degraded,
- Prior to cleaning, there were severe deposits in the system,
- More than 10% of the oil-cleaner mixture remains after draining.
Complete draining of all the old oil and cleaner mixture, including trapped mixture, helps mitigate the negative impacts on new oil performance and can reduce the need for flushing.
VARTECH ISC was formulated to be highly compatible with modern high-quality lubricants to minimize the risks of an incomplete drain or rinse.
That depends on the complexity of your system and the capabilities of your team. Simply adding the cleaner, operating the system, and then performing a thorough oil change can be an effective approach. A service provider often brings valuable experience and can be very beneficial in confined space entry for reservoir wipe down, certified oil disposal, filter changes, and providing auxiliary heat for offline cleaning. They can also aid in determining cleaner residence durations and application concentrations.
When in doubt, contact our Sales Representatives to help guide you.
Complement with our Services
-
Reliability-Based Lubrication Program
Help your equipment and operations run more reliably, efficiently and profitably with our RBL Program. We’ll show you how to reduce costs with the right products, services and knowledge.
-
LubeWatch® Oil Analysis: Advanced lab analysis to improve your operation
As you optimise your lubrication program for peak protection and performance, attentive monitoring helps you continue to achieve the benefits. LubeWatch oil analysis helps you detect potential problems and fine-tune your maintenance practices to extend drain intervals, minimize failures and reduce costs.